The Essence of Flexo Tech Process
Before we make the rotogravure vs flexographic comparison, let’s describe each solution in more detail. The latter technique implies that a photopolymer form is used to squeeze a special colored substance onto surfaces/materials designed for shading. A roller is used to allow the ink to penetrate the plate. Microscopic cells are made on the roller’s surface. These cells hold the ink and give it to plates upon contact. Here, several types of machines are distinguished. These are inductor and doctor blade machines. In inductor hardware, a rubberized shaft is used to catch the ink from the bath and redirect it to the anilox roller. A squeegee is placed in such equipment. This is a steel or plastic carrier that is installed along the entire transverse surface and removes excess paint. The process of functioning of the second type of equipment is based on feeding the ink directly onto the anilox roller, entering the doctor blade chamber. This is a closed space bounded by two doctor blades and soft end caps that act as glands. The paint of the required viscosity is fed by gravity into the doctor blade chamber and “wets” the anilox roller.
Materials to which Flexo Process is applied
The variety of materials used for this technology can be divided into several main groups: Thus, the solution is applied to all kinds of flexible packaging used for food and goods.
The Key Factors about Rotogravure Tech Process
To understand the difference between flexographic printing vs rotogravure, let’s consider the second technology. For this method, special metal shafts are used. An image is applied to their surface using a laser. Further, images are transferred to the material. Unlike flexo presses, the gravure press does not use an inductor roll. After the paint is applied to the surface of the shaft, its excess is removed using a special plate. The ink fills all the cells on the surface of the shaft, after which it is redirected to the material. During the rotogravure tech process, five main colors are used, with which you can achieve any shade of the image. But often, there is no need to use all five, and the desired shades are created from fewer colors. This also happens when the material on which the images are to be printed is initially white. Then you do not need to print a white “substrate”, which simplifies the process of applying images. Thanks to the use of volatile solvent-based inks, which provide fast drying, high printing speeds are achieved. In addition, this method is characterized by ideal image repeatability in repeated print runs. Today, gravure technology is one of the most popular ways to produce large circulations of printed products – packaging, bags, or sealed films.
Materials to which Rotogravure Technology is applied
Rotogravure presses are used to print on flexible materials such as:
aluminum foil; cardboard; paper; shrink PVC; polyethylene.
Flexo VS Rotogravure Technologies: Comparison
Now, let’s compare flexo vs rotogravure printing. The main similarity is that both solutions are widely used for labeling packaging and applying all sorts of images (logos, QR codes, guides, etc.) on wrapping. As for differences, there are three factors that prevent a rotogravure technology from competing with flexo one: In addition, add another problem associated with the inconvenience of storing rotogravure shafts. After all, they are quite bulky, and each order needs a separate shaft, so the equipment takes up more space and results in a complicated transportation. The cost of manufacturing printing plates is lower, and the speed of their production process is much higher. This feature allows printers using the flexo method to quickly respond to customer requests and significantly reduce the lead time. In comparison, the production of gravure cylinders takes about two months. Meanwhile, it is possible to make a flexo plate, test it, and start printing within one day. The manufacturing of flexible wrapping is not only about printing. Thus, when comparing flexography vs gravure printing, it is worth paying attention to the post-printing processes, which include various operations aimed at giving the package certain consumer properties. Such processes include laminating, applying various coatings, embossing, varnishing, cutting, and so on. Modern technologies allow them to be integrated into one line with both flexographic and gravure printing machines. According to statistics, the ratio of the volume of packaging sealed by these methods, as a whole, is approximately 50 to 50% worldwide. At the same time, one should keep in mind that flexographic technology is developing at a very fast pace and is constantly striving to get closer in quality to the second regarded type, which, unlike flexography, is rather conservative. To summarize the article, note that flexographic technology is an alternative method to gravure one. Its quality is close to gravure, but the whole process of production costs less. The use of flexo printing is very beneficial, given the high productivity of this technology. Δ Contact Us :- trendblog.guest@gmail.com
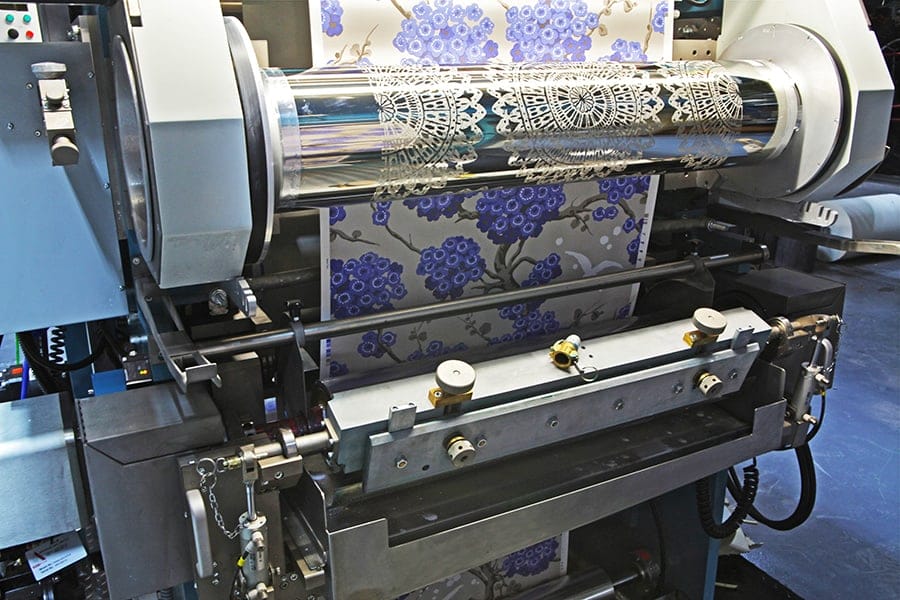